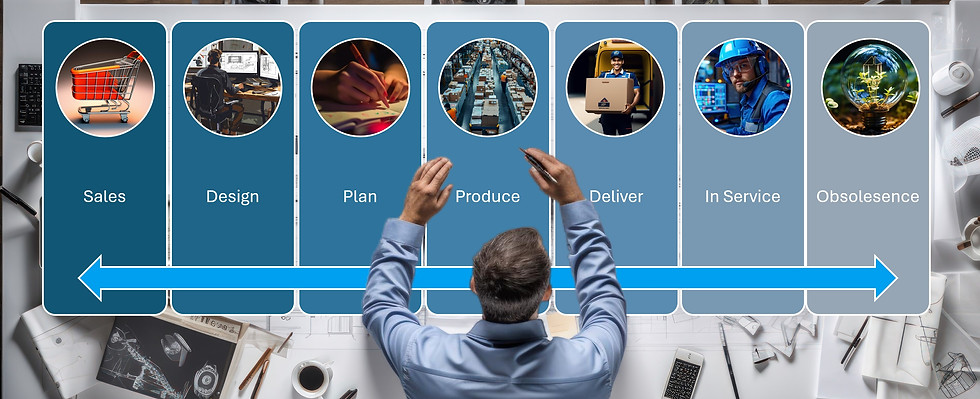
Operational processes

Reading time: 12 min

March 5, 2024
AUTOR
Pascal NAPARTY
CEO and Founder
In a nutshell
The functioning of a company is described by the operational (or discipline) processes which provide value to the customer, the support processes which are necessary for the realization of business processes and the management/steering processes which allow management to take decisions concerning the life of the company and its future.
Operational processes are the muscle of the company and can be grouped into 7 main categories that interact with each other.
​
Each business process describes the responsibilities of the stakeholders but also the data flows.
Process mapping provides a clear view of how the business is functioning and helps isolate areas of slowdown, where improvement or support will be needed.
Among the business processes we distinguish: The sales cycle, The product development process (PDP), the manufacturing process, the delivery process, the customer support process, etc.
The support processes support operational processes, we distinguish for example: The recruitment process, The training process, The payroll process, The process of reimbursement of expenses incurred by employees, The equipment maintenance process, etc. .
Introduction
Navigating the operation of a business is not a simple thing. Many companies do not document all of their operational processes due to lack of time and resources.
​
The knowledge then resides in the men and women who carry out the work with a legacy of word of mouth. Difficult to transmit knowledge and give a form of delegation of work to teams if the description of the tasks (why, what, who, when, how, where) is poorly transcribed because "Rain Maker" is not available.
​
Without documenting the process it is difficult to initiate actions to optimize performance because we cannot compare the current with the theory. We can only compare a current trend with the past. However, a diagnosis of the problem could reveal a malfunction prior to the problem observed.
​
In this study we will broadly explain the fundamental professions and their responsibilities in the overall operational process.
​​
What is a process?
A process (or workflow) is a set of organized steps and tasks designed to achieve a given objective.
​
Each process is designed to answer the following questions: what ? who ? when ? how ? It thus links data to the parties involved in carrying it out, ensuring repeatability and standardization of tasks.
​
A well-developed process brings great value to organizations, enabling optimization of resources and improved results. Lower-value tasks can be automated or outsourced, for example. Teams can concentrate on value-added tasks and avoid stress crises.
​
Process management tools and/or methodologies include :
-
Process management - using BPM-type modeling,
- Checklists - to ensure that no stage has been overlooked,
- Gantt charts - for visual project management,
- Flowcharts/synopses - for a sequential view of activities.
A typical operating process
​
In consulting, we seek to represent and simplify in an attempt to answer questions and define priorities and urgencies. When we look at an operational process as a whole, we can summarize it in major phases or views. Each one has a specific purpose.
This approach is taken from the aeronautics industry, which describes the complexity of its operational processes in terms of views. This enables the many people involved to converge and make the right decisions when executing tasks.
The main views are :
-
The "as-sold" view, this phase, which is the responsibility of the sales teams, defines and documents the product's requirements and physical characteristics. Example: The motor must be able to start at -30 C and +45 C. If the product does not meet this requirement, it will not be accepted by the buyer, and the seller will certainly incur penalties.
-
The "as-designed" view, this phase defines in detail the studies carried out by engineers to design the purchased product. The 3D or 2D modeling of the product, its simulation in linear, non-linear, fluidic, magnetic resistance... and the documentation of the study results lead to the stage of preparation for manufacturing. Obviously, this is a little more complicated, and many disciplines are involved in the product. They all need a collaborative platform to consolidate their studies and confirm that the work is fully completed and compliant with customer expectations and current regulations.
-
The "as-planned" view, this phase consists of production planning, and is carried out by a methods office under the responsibility of production. The information supplied by the design office is taken into account. Drawings are adapted for use in production, and the necessary resources are defined. Build assembly lines. List the tools and materials required. Select the plant and cells required for machining or assembly. We use software to simulate the operation of the whole system and anticipate potential problems. We simulate working conditions to maximize productivity. We refine budgets and feed forecast orders into purchasing. We inform human resources of specific skill requirements. Identify risks and propose crisis management plans.
-
The "as-built" view, this phase consists of manufacturing and demonstrating compliance with the instructions in the construction/assembly schedule. Materials are received. We number them after inspection. Everything is listed in the manufacturing bill of materials. Quality is tracked to ensure that every weld, bolt and rivet has been placed as agreed, using the correct technique and/or torque. Over time, certain parts are improved (we try to make them lighter, change the material, etc.). However, we need to be able to return at any time to a particular configuration delivered to a customer in the past... so that we can perhaps manufacture to order a part that has reached the end of its life.
-
The "as-shipped" view, this phase consists of defining the product's shipping conditions. Here we define the packages (wooden, foam and plastic crates, user documentation, maintenance documentation, etc.) that must accompany the product, as well as the specific requirements for certain regions or countries.
-
The "as delivered" view, this phase enables you to trace the conditions of delivery and receipt of the product. It may also be necessary to carry out commissioning for the customer, and to train the customer. Delivery is therefore the set of services that accompany the delivered product. It may also be agreed in the "as-sold" view that an advanced level of maintenance will be provided by the seller, and therefore the seller may seek to capture information relating to the location and conditions of use of the product.
-
The "as-maintained" view, this phase involves managing difficulties in use, replacing end-of-life parts, preventing breakdowns and maximizing product productivity. During the design phase, the engineering department not only designs the product, it must also design it so that it can be manufactured and maintained. Sometimes, it produces specific tools that will be useful for maintenance. He always provides maintenance instructions. The customer (if he does not have a maintenance contract with the vendor), will have to ensure compliance with updates and replacement of parts according to the vendor's recommendations. As modifications are made, the product documentation must also be updated, as its configuration has changed... new parts have been added.
-
The "as-recycled" view, this final phase of the operational process addresses product obsolescence and component recycling. It includes teams and specific instructions for disassembling products and recycling components... Think of a nuclear power plant: at the end of its life, special tools and machines are needed, as well as protection for the workers, to dismantle the plant and isolate the components. They will all follow a circuit for cleaning and recycling... or storage for decontamination.
Business process modeling (BPM)
Business Process Management is a methodology implemented by companies and used by management and business teams. It visually describes the flow of activities required to complete a job. It identifies the stakeholders and highlights the inputs and outputs at each stage, as well as the tools and systems required for smooth operation.
This representation helps to simplify understanding and align teams. Analysis of each task/flow provides avenues for continuous improvement, helping the company to become more efficient.
Each department may be responsible for setting up its own business process management system. But it is also common to see a single team dedicated to this task, interacting with all departments.
It's worth noting that some customers demand traceability and proof of flawless recurring execution in their purchasing conditions. In such cases, BPM is essential, enabling the implementation of a repository that eliminates any ambiguities for all parties involved.
Tools and systems
​
The process provides a clear understanding of the sequence of activities and stakeholder involvement at a given point in time. It also enables the process itself to be optimized. It doesn't optimize the efficiency of each task at its elementary level, which requires the definition of contextual strategies or tactics.
​
It's important to bear in mind that every man and woman who contributes to the process does so with his or her own level of knowledge, skills and the tools at their disposal.
​
Process modeling highlights the data required "in" and the data expected "out" of the task.
Additional questions need to be asked to make the process optimal:
-
How does the operator access the data?
-
How long does it take to find it?
-
Is he working with the right version of the information?
-
Does it have the context to make a decision?
-
Does it have the expertise and the best tools/technologies to produce the expected output?
-
How does he contribute to the justification of his task?
-
How much time does it take?
-
How can we measure his actions to help him be optimal?
​​
It is this approach that will enable the company to identify common needs and implement (1) process changes or (2) digital transformations or (3) training that will support people in their day-to-day work ... or even (4) propose changes to the organization.
​
Tools and systems therefore need to be viewed with an expert eye, just like processes and people.
Conclusion
The company's referential involves defining and documenting business processes. It must be made accessible to all employees. We do well what we understand well. As the company evolves, it is important to regularly review all processes and to update this referential.
Management teams play a key role in disseminating information and reminding people of the rules.
The benefits for the company that implements and uses this methodology are :
-
Better team alignment,
- Clear expectations,
- Better guidance for management,
- Introduction of continuous improvement,
- Review of tools and systems,
- Training staff with,
- Smooth execution,
- Improved quality,
- Cycle optimization ,
- Improved margins